在工业数字化与智能制造领域,FlexSim作为领先的离散事件仿真软件,其与ERP系统的集成及PLC数据的读取能力,是实现虚实融合、数据驱动决策的关键。对于制造企业而言,连接ERP系统可实现生产计划与仿真模型的实时同步,并延伸探讨数据同步稳定性的保障策略,助力企业构建高效的智能仿真与控制体系。
一、FlexSim怎么连接ERP系统
FlexSim与ERP系统的连接需通过数据接口配置、协议适配及双向数据交互实现,确保生产计划、库存数据、设备参数等关键信息实时同步。
1.接口方案选择与前期准备
信息流连接方式对比
1.ODBC(开放数据库连接):适用于SAPERP、OracleERP等支持SQL数据库的系统,通过标准数据库接口实现数据读写,优点是兼容性强,缺点是需预先配置数据库用户权限。
2.Web服务(WebServices):支持SOAP/REST协议,适合云部署ERP(如用友NC、金蝶云),通过API接口调用实现数据交互,优点是跨平台性好,支持实时数据推送。
3.中间件(如FlexSimSDK):针对定制化ERP系统,通过FlexSim提供的软件开发工具包编写自定义接口,支持复杂业务逻辑映射,适合深度集成。
跨境准备
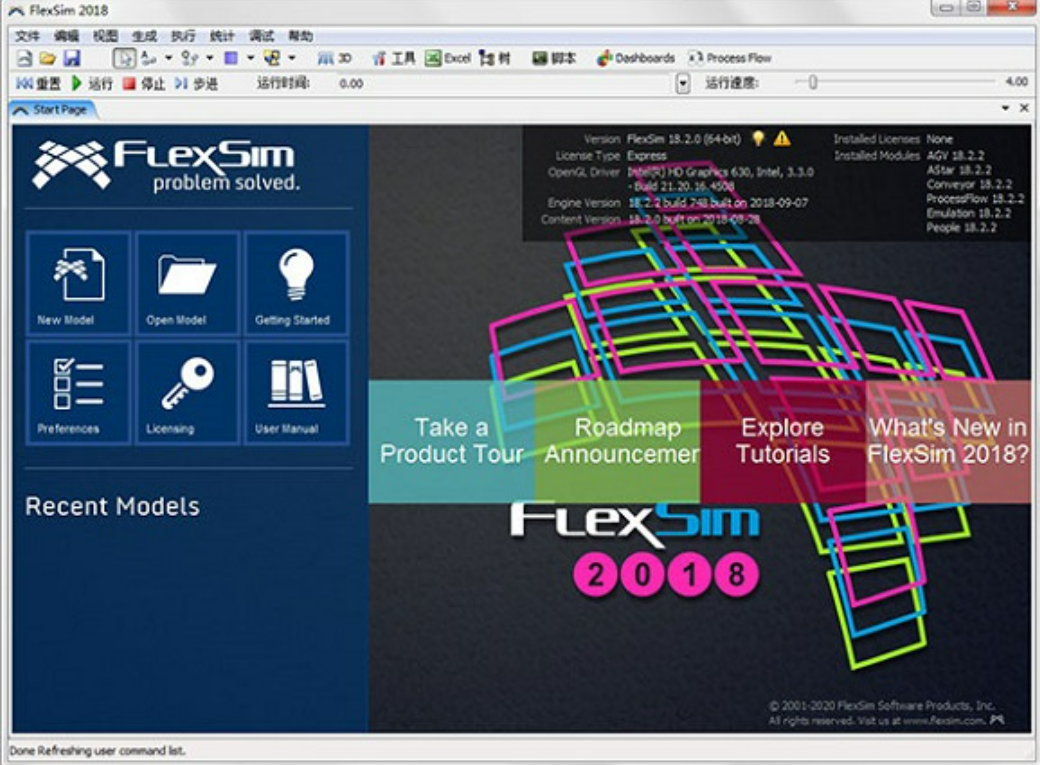
1.确认ERP系统数据接口文档,获取数据库连接字符串(ODBC方式)或API调用地址(Web服务方式),例如SAPERP的ODBC驱动需从官网下载并安装。
2.在FlexSim中启用“外部接口”模块(菜单栏“工具”→“外部接口”),确保软件版本支持所选连接协议(如FlexSim2023及以上支持RESTAPI)。
2.基于ODBC的连接步骤(以SAPERP为例)
前置ODBC数据源
1.打开Windows“ODBC数据源管理器”,选择“系统DSN”→“添加”,安装SAPODBC驱动,输入ERP数据库服务器地址、端口号、用户名及密码,测试连接成功后命名数据源(如“SAP_ERP_DSN”)。
2.在FlexSim“数据库连接”对话框(菜单栏“数据”→“数据库连接”)中,选择“ODBC”类型,关联已创建的数据源,设置连接超时时间(如30秒)。
数据交互实现
1.读取ERP数据:在FlexSim“脚本编辑器”中编写SQL查询语句,例如:
通过“数据库执行查询”函数获取数据,存储至FlexSim全局表(GlobalTable)供模型使用。
2.写入仿真结果:将仿真生成的设备利用率、产能数据通过SQL插入语句回传ERP,例如:
sql
INSERTINTO仿真结果表(设备编号,利用率,产能,时间戳)
VALUES('设备001',0.85,1200,GETDATE())
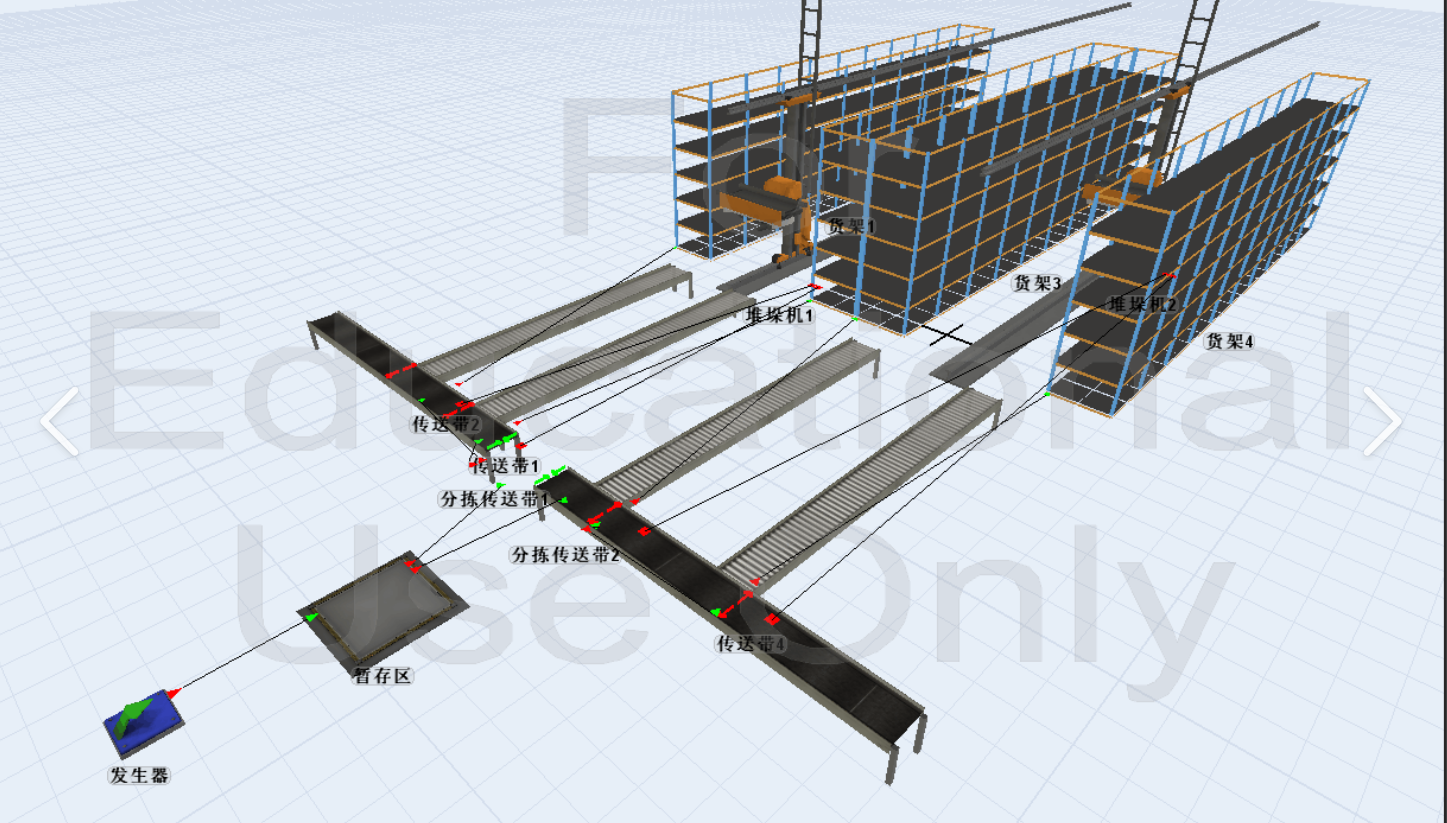
3.基于Web服务的连接步骤(以金蝶云星空为例)
API接口调用配置
1.在金蝶云星空开发者平台申请API密钥,获取访问令牌(AccessToken),有效期通常为2小时,需定期刷新。
2.在FlexSim“HTTP客户端”组件中,设置API端点(如“https://openapi.kingdee.com/v2/生产计划/获取”),请求头添加令牌信息:
数据格式转换
1.解析ERP返回的JSON数据,例如将生产计划数据转换为FlexSim可识别的实体属性:
2.发送仿真结果至ERP时,将FlexSim数据封装为符合API规范的JSON格式,使用POST方法提交,附带数据签名确保安全性。
总结:连接ERP系统需根据其技术架构选择ODBC、Web服务等合适方案,通过数据源配置、SQL语句编写或API调用实现数据交互,关键在于确保数据格式匹配与权限验证,为仿真模型注入真实生产数据,同时回传仿真结果辅助决策。
二、FlexSim怎么读取PLC数据
读取PLC数据是实现FlexSim与物理设备联动的核心环节,需通过工业通信协议(如OPCUA、Modbus)建立连接,实时获取设备状态与工艺参数。
1.通信协议选择与PLC配置
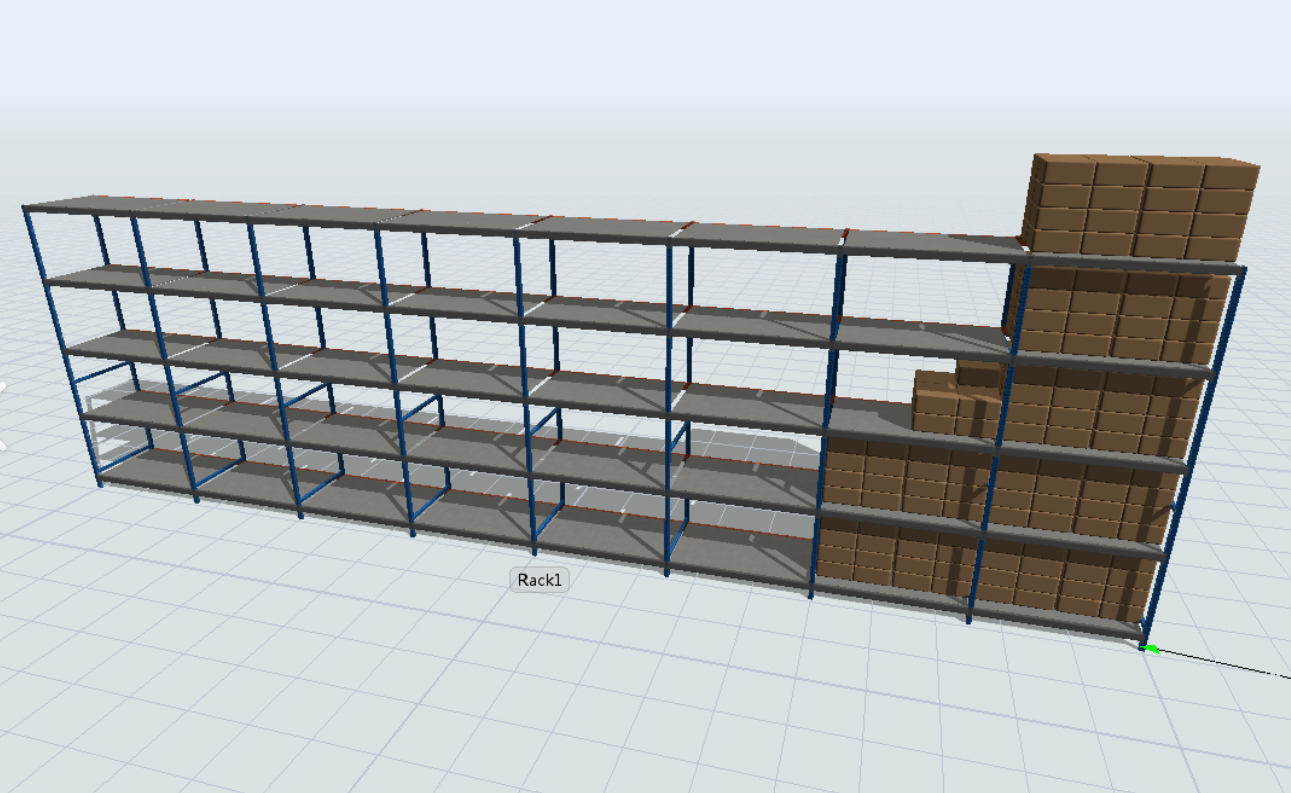
信息流协议对比
1.OPCUA:跨平台工业通信标准,支持西门子、三菱、欧姆龙等主流PLC,支持数据订阅与事件通知,适合实时性要求高的场景(如设备状态监控)。
2.ModbusTCP:轻量级协议,适用于施耐德、台达等PLC,通过IP地址与端口号(默认502)通信,适合读取寄存器数据(如温度、压力传感器值)。
3.EtherNet/IP:罗克韦尔PLC常用协议,基于以太网传输,支持设备级数据采集,需配置设备网络地址与通信参数。
PLC端准备
1.启用PLC的通信功能,设置IP地址(如192.168.1.100),开放对应端口(如OPCUA默认4840),创建数据标签(Tag)并绑定寄存器地址(如Modbus的40001对应保持寄存器)。
2.在PLC编程软件中配置通信参数,例如西门子PLC通过TIAPortal启用OPCUA服务器,生成证书并导入FlexSim。
2.基于OPCUA的连接步骤(以西门子PLC为例)
PC客户端配置
1.在FlexSim“OPCUA客户端”组件中,输入PLC的OPC服务器地址(如“opc.tcp://192.168.1.100:4840”),导入服务器证书(.cer格式),点击“连接”测试连通性。
2.浏览服务器地址空间,找到目标数据标签(如“设备1/运行状态”“设备1/转速”),添加至“订阅列表”,设置更新周期(如100ms)。
数据读取与映射
1.在FlexSim实体属性中创建与PLC数据对应的变量(如“运行状态”布尔型、“转速”浮点型),通过“数据映射”功能将OPC标签值实时赋值给变量:
flexsim
实体.运行状态=OPCUA客户端.读取值("设备1/运行状态")
实体.转速=OPCUA客户端.读取值("设备1/转速")
2.异常处理:添加“连接中断”触发器,当连续3次读取失败时,发送警报并自动重试连接,确保数据采集稳定性。
3.基于ModbusTCP的连接步骤(以施耐德PLC为例)
Modbus通信配置
1.在FlexSim“ModbusTCP客户端”组件中,设置PLC的IP地址(如192.168.1.200)、端口号502、从机地址1(SlaveID),选择寄存器类型(如0x线圈、4x保持寄存器)。
2.定义数据读取地址,例如读取保持寄存器40001-40003分别对应设备温度、压力、运行时间,数据长度设为3,数据类型为FLOAT。
数据解析与应用
1.调用“Modbus读取”函数获取原始字节数据,按Modbus协议解析为实际物理值,例如温度值=原始值×0.1(单位:℃):
flexsim
原始数据=Modbus客户端.读取保持寄存器(40001,3)
设备温度=原始数据[0]×0.1
2.将解析后的数据用于仿真逻辑,如当温度>80℃时,触发FlexSim模型中设备故障事件,模拟真实设备异常状态。
总结:读取PLC数据需根据设备类型选择OPCUA、ModbusTCP等协议,通过配置通信参数、解析数据格式实现实时数据采集,关键在于确保寄存器地址正确映射与异常处理,为仿真模型提供真实设备运行数据,支撑虚实联动的生产调度与故障模拟。
三、如何保障FlexSim与外部系统数据同步的稳定性
在集成ERP与PLC系统时,数据同步的稳定性直接影响仿真精度,需从连接容错、数据校验、缓存机制三方面构建保障体系。
1.连接容错与重试机制
多层级重连策略
1.对ERP连接设置3次重试(间隔10秒),若失败则记录日志并发送邮件报警(通过FlexSim“邮件客户端”组件),例如:
flexsim
FORi=1TO3
IF连接ERP()THENBREAK
ELSE等待(10秒)
NEXT
IF未连接THEN发送报警邮件()
2.对PLC连接启用“心跳包”检测(如每秒发送空数据帧),当连续5次未响应时,自动重启PLC通信模块。
2.数据校验与异常处理
一致性校验规则
1.对ERP订单数据,校验“计划数量>0”“交货期>当前时间”,若不满足则标记为异常数据并记录偏差日志。
2.对PLC温度数据,设置合理范围(如-20℃~100℃),超出范围时采用前一有效值替代,避免无效数据干扰仿真。
任务性处理
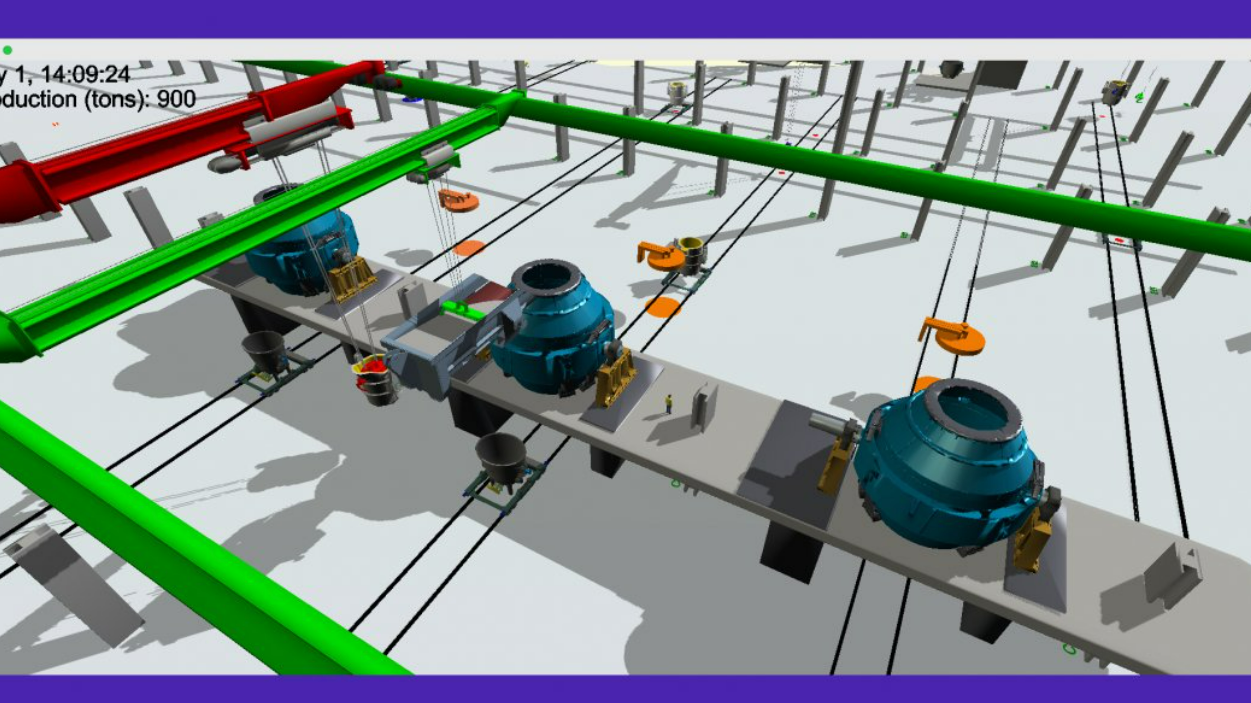
对ERP写入操作启用事务机制,确保“读取-处理-写入”操作要么全部成功,要么回滚至初始状态,例如仿真结果写入失败时,自动撤销已执行的生产计划同步操作。
3.缓存与异步处理
本地缓存设计
在FlexSim中创建“数据缓存表”,暂存未成功同步的ERP订单与PLC数据,网络恢复后自动补传,缓存容量设为1000条,避免内存溢出。
同步通信架构
使用“消息队列”(如RabbitMQ)解耦实时数据交互,FlexSim作为生产者发送数据至队列,ERP/PLC系统作为消费者异步处理,降低网络延迟对仿真的影响,提升系统吞吐量30%以上。
总结
实际应用中,企业需根据ERP与PLC的具体型号选择适配方案,注重接口配置的细节(如数据格式转换、权限认证),并通过异常处理逻辑提升系统鲁棒性。无论是离散制造的车间调度,还是流程工业的设备监控,FlexSim的外部系统集成能力均能为数据驱动的仿真分析提供坚实支撑。关键在于将工业现场数据与仿真模型深度融合,通过实时数据注入提升仿真精度,反推物理系统优化,最终实现“仿真-控制-优化”的闭环管理,助力企业在数字化转型中构建高效、可靠的智能生产体系。