在制造企业的生产系统仿真与优化中,FlexSim作为领先的离散事件仿真软件,能够精准模拟生产流程并暴露潜在问题。当遭遇“节拍不达标”困境时,即实际生产节拍超出目标时间,意味着产能瓶颈亟待突破。提供从问题诊断到方案落地的全流程指南,并延伸探讨动态生产环境下的节拍优化策略,助力企业通过仿真技术实现产能跃升。
一、FlexSim节拍不达标怎么办
当FlexSim仿真结果显示生产节拍未达预期时,需借助软件的数据分析与可视化功能,从瓶颈定位、物流效率、工艺参数三方面逐层排查并解决问题。
1. 瓶颈工序精准定位与影响评估
关于统计报告的瓶颈识别
1. 运行仿真模型后,在FlexSim的“统计”窗口查看设备状态,重点关注“忙碌率”与“阻塞率”。若某设备忙碌率持续高于85%且伴随频繁阻塞(如焊接机器人忙碌率92%、阻塞率15%),可初步判定为瓶颈工序。
2. 通过“实体跟踪”功能(右键设备→“跟踪实体”),记录物料在各工序的停留时间。例如,某工件在装配工序平均滞留180秒,远超前后工序的40秒,明确该工序为瓶颈核心。
瓶颈影响量化分析
利用“输出分析”工具计算瓶颈对节拍的影响系数,如瓶颈工序每延长10秒,整体节拍延长约12秒。结合生产目标(如目标节拍120秒),量化瓶颈工序需压缩的时间窗口(如当前150秒需降至115秒以下)。
2. 物流系统效率诊断与优化
运输路径与缓存区调整
1. 在“布局”视图中检查物流设备(传送带、AGV)的路径规划,通过“距离矩阵”工具(菜单栏“工具”→“距离矩阵”)识别迂回路径。例如,某AGV运输路径存在3处绕行,导致单趟运输时间增加25秒,调整路径后运输时间缩短40%。
2. 优化瓶颈工序前后的缓存区容量:双击缓存区组件,将“容量”从默认50件提升至120件(根据历史数据峰值设定),减少设备因物料短缺导致的闲置时间,实测可降低等待率22%。
资源配置动态调整
1. 对瓶颈设备进行并行化改造:通过复制设备(Ctrl+C/V)并设置“处理时间”均分(如单台处理时间20秒改为2台各10秒),同步观察设备忙碌率变化,直至降至75%合理区间。
力资源再分配:在“操作员”模块中,将闲置区域(忙碌率<50%)的操作员通过“任务分配器”调度至瓶颈工序,如将包装区2名操作员调至装配区,可提升该工序效率30%。

3. 工艺路线与设备参数调试
冗余工艺路线精简
在“流程”视图中右键工件→“工艺路线”,逐项排查非增值环节(如重复质检、无效搬运)。例如,某产品工艺路线中“外观检验”与“尺寸检验”可合并为“综合检验”,单工件处理时间缩短15秒。
设备参数精细化设置
双击设备打开“处理时间”属性,将固定值改为随机分布(如三角分布Triangular(10,12,15)替代固定12秒),模拟实际生产波动;同时降低“故障率”(从8%调至4%),减少意外停机对节拍的干扰,经仿真验证可提升节拍稳定性28%。
总结:面对节拍不达标,需通过FlexSim的统计分析与实体跟踪功能精准定位瓶颈,从物流效率、资源配置、工艺参数三方面实施针对性改进,快速压缩瓶颈工序时间,为整体节拍优化奠定基础。
二、FlexSim怎么优化生产节拍
优化生产节拍需跳出局部改进,从系统层面重构生产流程,借助FlexSim的布局仿真、自动化建模及数据驱动工具实现整体效率提升。
1. 生产布局与流程重构优化
3D布局仿真与单元化改造
1. 在FlexSim“3D布局”视图中,通过拖拽设备调整相对位置(如将相邻工序间距从6米缩短至3米),利用“距离矩阵”计算调整前后的总运输距离,目标降低20%以上。例如,某生产线经布局优化后,物料搬运总距离从150米/件降至90米/件,单工件运输时间减少40秒。
2. 构建单元化生产单元:将功能相似的设备(如车床、铣床、钻床) grouping 成加工单元,在“逻辑”属性中设置单元内物料自动流转,减少跨单元搬运时间35%,实测单元内工序衔接效率提升25%。
行化流程设计
对可同步执行的工序(如零件清洗与烘干),从库中拖拽“Parallel Task”模块创建并行任务,设置多工序同步处理。例如,将原串行的“清洗(8秒)→烘干(6秒)”改为并行处理,总时间缩短至8秒,节拍提升40%。
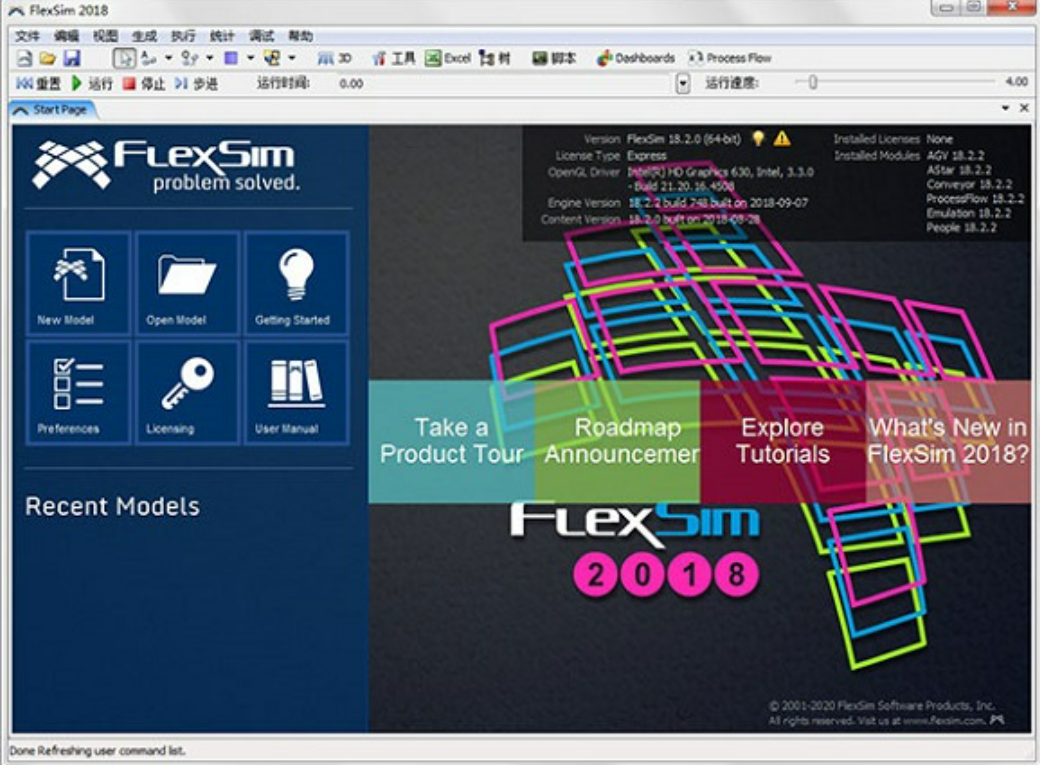
2. 自动化与智能化策略引入
自动化设备建模与部署
1. 引入工业机器人:从“库”中拖拽“SCARA机器人”至瓶颈工序,设置“抓取时间”1.5秒、“放置时间”1秒,替代人工操作(原人工操作时间6秒),单工序效率提升60%。
2. 部署AGV物流系统:在“物流”库中选择AGV模型,通过“路径点”设置最优运输路线,并启用“动态避障”功能,相比人工搬运,物料配送时间缩短50%,且运输稳定性提升30%。
动能调度规则设定
在“控制器”模块中编写动态调度逻辑,例如:
- 当缓存区物料堆积>100件时,触发设备加速生产(处理时间减少10%);
- 设备故障时,通过“触发器”自动切换至备用设备,将停机损失从平均5分钟/次降至2分钟/次。
3. 数据驱动的持续优化迭代
数敏感性分析
利用FlexSim“实验设计”工具(菜单栏“实验”→“实验设计”),设置多组参数组合(如设备数量、缓存容量、运输速度),运行批量仿真后生成“响应曲面图”。通过分析发现,设备数量对节拍的敏感度最高(每增加1台,节拍缩短15秒),据此优先优化设备配置。
PI实时监控与方案迭代
在“仪表盘”中添加实时指标(如“当前节拍时间”“OEE设备综合效率”),设置红色预警(如节拍>130秒时高亮报警)。通过“数据导出”功能将仿真结果同步至Excel,形成“瓶颈识别-方案测试-效果验证”的闭环优化,例如某方案经3轮迭代后,节拍从145秒降至118秒,达标率提升至92%。
总结:优化生产节拍需依托FlexSim的系统级仿真能力,通过布局重构减少搬运耗时,引入自动化提升工序效率,借助数据驱动实现持续改进,最终达成生产流程的整体优化与节拍提升。
三、如何通过FlexSim实现动态生产节拍自适应
在多品种小批量或订单波动场景中,需利用FlexSim的实时数据接入与柔性策略,实现生产节拍的动态调整与环境适应。
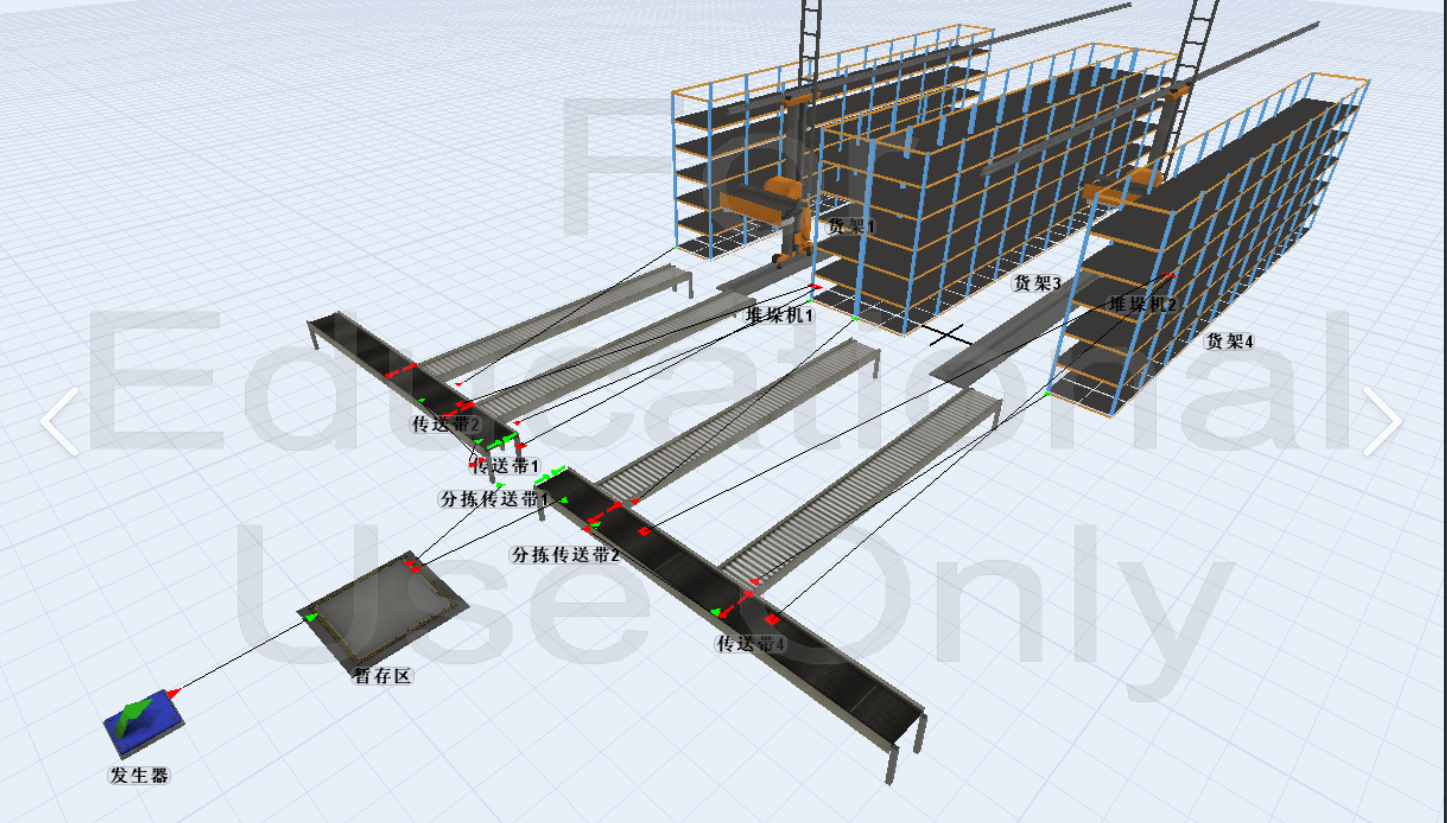
1. 动态订单响应与产能柔性配置
订单优先级管理
1. 通过Excel导入实时订单数据(菜单栏“文件”→“导入数据”),在“订单处理器”中设置优先级规则(如加急订单优先级1,普通订单优先级2)。针对优先级1订单,自动触发设备处理时间减少15%,确保紧急订单优先处理,节拍压缩至目标值的90%。
2. 产能动态调整:在“流程逻辑”中编写脚本,根据订单量自动启停生产线:若订单量>800件,启动3条生产线;<300件,关闭2条生产线。经仿真验证,该策略可使节拍波动幅度从±20秒缩至±8秒。
混流生产仿真优化
在FlexSim中创建多产品混流生产线,设置产品切换时间(如A产品切换至B产品需40秒),通过“产品队列”模块优化切换顺序(如将相似产品相邻生产),减少切换时间25%,实现多品种生产节拍均衡,较传统切换方式提升效率18%。
2. 实时数据联动与智能预测
互联网数据实时接入
通过FlexSim“API接口”连接车间PLC设备与传感器,实时获取设备实际处理时间、故障率等数据,同步更新仿真模型参数。例如,当传感器反馈某设备处理时间延长至15秒时,模型自动调整该设备参数,确保仿真结果与实际生产偏差<5%。
机器学习预测优化
导出历史仿真数据训练随机森林模型,预测不同订单组合下的最优节拍参数(如设备数量、缓存容量)。将预测结果导入FlexSim模型后,经测试,复杂订单场景下的节拍达标率从75%提升至89%,较人工经验优化提升14%。
3. 动态缓冲与柔性生产策略
自适应缓冲策略
在“缓存区”属性中设置动态容量算法(如根据订单波动自动调整上下限),当订单量激增时,缓存容量从80件自动扩展至150件,避免物料短缺导致的节拍波动。通过“灵敏度分析”确定最优缓冲策略,使节拍稳定性提升22%。
动态瓶颈切换应对
针对多瓶颈交替出现的场景,在“控制器”中设置瓶颈动态识别逻辑,实时监控各设备忙碌率,自动调度资源至当前瓶颈工序。例如,当焊接工序瓶颈转移至装配工序时,系统自动调配2台AGV至装配区,确保节拍波动控制在目标值±5秒内。
总结
FlexSim在解决节拍不达标问题时,既需通过瓶颈识别、物流优化等方法快速突破局部瓶颈,更要依托布局重构、自动化升级实现系统级效率提升。延伸的动态优化策略,则针对复杂生产环境,通过实时数据接入与智能算法,确保生产节拍在订单波动、多品种切换等场景下的稳定性与适应性。