在物流系统规划与仿真领域,FlexSim凭借其强大的离散事件建模能力,成为量化输送机输送能力、验证物流方案可行性的核心工具。对于制造业与仓储物流企业而言,精准计算输送机能力可确保物料流转效率,而科学验证物流方案则能提前规避设计缺陷。
一、如何用FlexSim计算输送机能力
利用FlexSim计算输送机能力需通过模型构建、参数设置、仿真运行及数据提取,精准量化输送机在不同场景下的理论与实际输送能力。
1.输送机模型搭建与参数配置
备选型与布局

1.从FlexSim“物流库”中拖拽目标输送机类型(如辊道输送机、皮带输送机)至3D布局视图,根据实际尺寸设置“长度”“宽度”“高度”(如长度50米、宽度0.8米),并通过“连接端口”功能(右键输送机→“添加连接”)连接上下游设备(如货架、分拣机)。
2.参数初始化:双击输送机打开属性窗口,设置“速度”(如0.8米/秒)、“间距”(相邻物料最小距离0.5米)、“最大容量”(同时承载物料数20件),对于分拣输送机,需额外设置“分拣规则”(如按物料类型分拣至不同出口)。
料流定义
创建物料实体(菜单栏“实体”→“新建”),设置物料尺寸(长0.6米×宽0.4米×高0.3米)、重量(15kg)及生成规律(通过“发生器”设置到达间隔时间,如平均3秒/件,分布类型为指数分布),确保物料流符合实际生产节奏。
2.理论产能计算与仿真运行
论输送能力公式推导
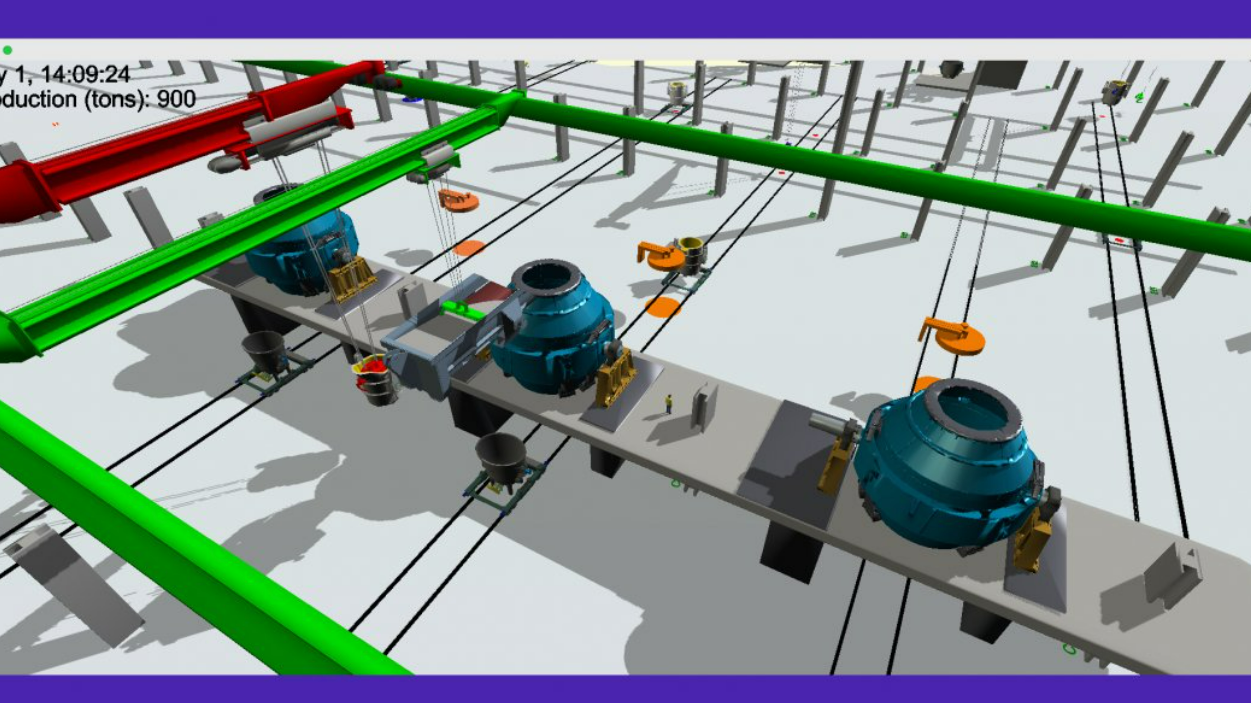
输送机理论产能(件/小时)=3600秒×速度(米/秒)÷物料间距(米),例如速度0.8米/秒、间距0.5米时,理论产能=3600×0.8÷0.5=5760件/小时。在FlexSim中可通过“计算器”功能(菜单栏“工具”→“计算器”)快速验证理论值。
真场景设置
1.运行时间设定:在“仿真控制器”中设置运行时长(如8小时工作制,3600×8秒),勾选“连续运行”避免中断。
2.数据采集开启:在输送机属性窗口“统计”选项卡中,勾选“启用统计”,记录“吞吐量”“堵塞次数”“空闲时间”等关键指标,为后续分析提供数据基础。
3.数据提取与能力分析
实时数据监控
运行仿真时,通过FlexSim“仪表盘”添加“输送机吞吐量”实时图表,观察曲线波动。若曲线在运行1小时后趋于稳定(如稳定在5500件/小时),说明实际产能接近理论值;若持续低于理论值(如4000件/小时),需排查堵塞或空载问题。
统计报告解读
1.运行结束后,在“统计”窗口筛选目标输送机,查看“吞吐量”“利用率”“平均负载”等数据。例如,某输送机利用率达92%、吞吐量5400件/小时,表明接近满负荷运行,需考虑扩容或提速。
2.瓶颈识别:若输送机下游设备(如分拣机)处理速度不足,导致输送机末端堵塞(堵塞次数每小时15次),则实际产能受限于下游,需同步优化分拣效率。
总结:计算输送机能力需从模型搭建、参数配置入手,通过理论公式与仿真运行双重验证,结合实时数据监控与统计报告分析,精准定位产能瓶颈,为设备选型与参数调整提供依据。
二、FlexSim怎么验证物流方案

验证物流方案需通过多方案建模、参数对比、指标分析,确保方案在效率、成本、稳定性上满足设计目标。
1.物流方案建模与变量设置
方案分层构建
1.基础方案:搭建包含“发生器-输送机-处理设备-吸收器”的基础物流链,输送机采用单线路径,处理设备为单台分拣机,参数设置为行业基准值(如分拣速度10件/分钟)。
2.优化方案:增加并联输送机(2条并行)、升级分拣机为高速型号(分拣速度15件/分钟),并在输送机中段增设缓存区(容量50件),形成对比方案。
变量控制与分组
通过FlexSim“实验设计”功能(菜单栏“实验”→“实验设计”),将输送机数量(1条/2条)、分拣速度(10件/分钟/15件/分钟)设为自变量,吞吐量、设备利用率、物料平均等待时间设为因变量,生成多组对比实验。
2.仿真运行与关键指标对比
方案并行运行
在“实验控制器”中设置方案运行次数(如每个方案运行10次取平均值),避免随机误差影响结果。例如,基础方案平均吞吐量4800件/小时,优化方案达6200件/小时,提升29%。
1.效率指标:吞吐量(件/小时)、设备利用率(%),优化方案输送机利用率从85%降至72%,表明产能冗余可应对峰值需求。
2.成本指标:通过“成本计算器”(需自定义设备折旧、能耗参数),计算方案运行成本,优化方案初期投资增加15%,但单位物料处理成本降低22%。
3.稳定性指标:物料平均等待时间(秒)、堵塞频率(次/小时),优化方案等待时间从45秒降至18秒,堵塞频率从12次/小时降至3次/小时。
3.可视化验证与风险识别
3D动态演示
通过FlexSim“3D视图”观察物料流动状态,基础方案中输送机末端频繁堆积物料(红色高亮显示堵塞),而优化方案中物料均匀分布,验证缓存区设置有效缓解堵塞。
灵敏度分析
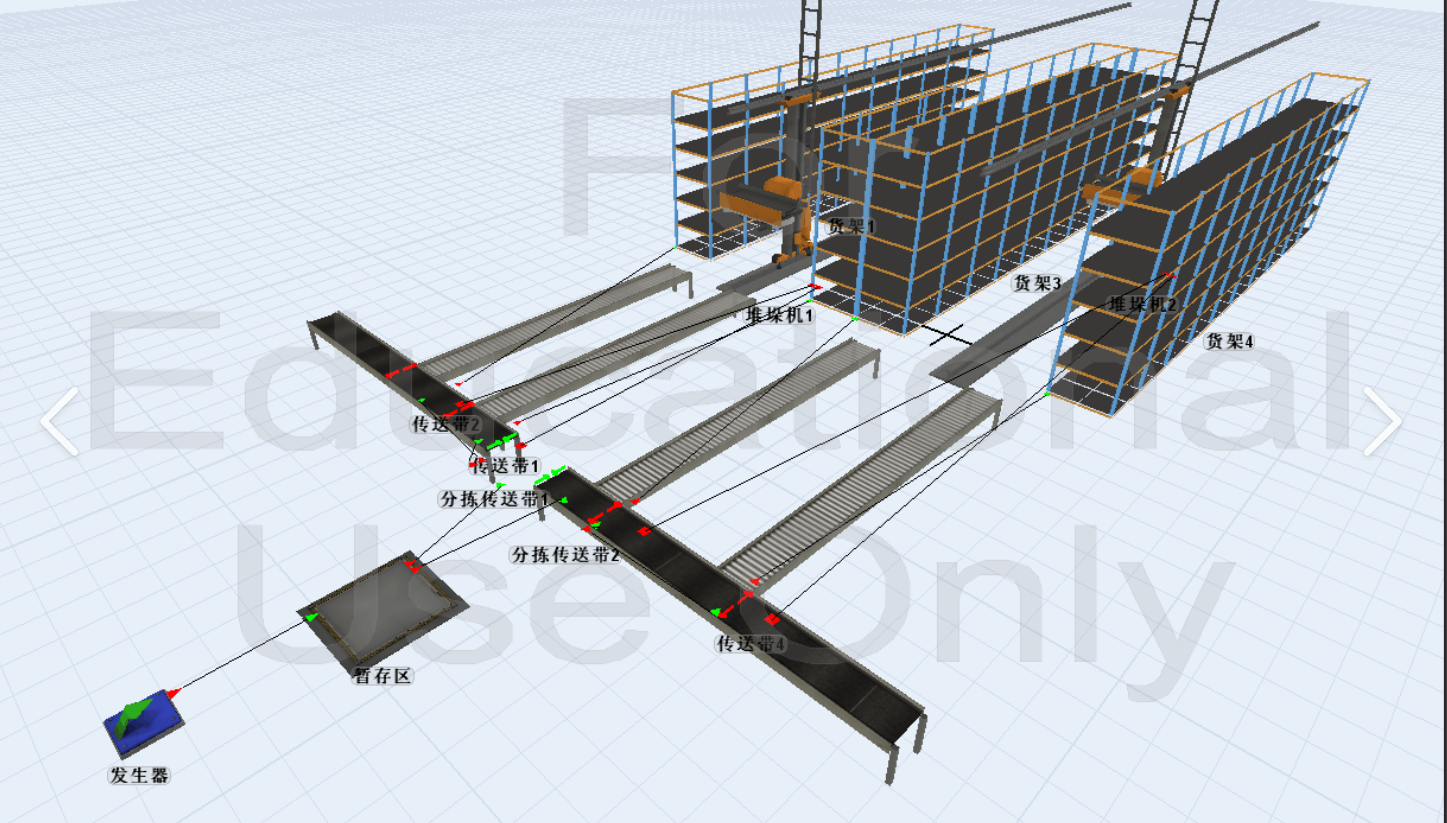
利用“响应曲面图”分析变量影响程度,发现分拣速度对吞吐量的影响系数为0.78(输送机数量影响系数0.52),表明提升分拣速度是关键优化点,与实际场景中分拣效率瓶颈相吻合。
总结:验证物流方案需构建多版本模型,通过控制变量、并行仿真、指标对比,结合可视化演示与灵敏度分析,从效率、成本、稳定性多角度评估方案优劣,确保设计方案既满足产能需求,又具备经济可行性与风险抵御能力。
三、如何通过FlexSim优化输送机与其他物流设备的协同效率
在复杂物流系统中,输送机需与AGV、货架、分拣机等设备协同工作,通过FlexSim可实现设备间的联动优化。
1.设备匹配与调度策略设计
AGV与输送机联动
1.在输送机两端设置“AGV停靠点”,通过“任务分配器”定义调度规则:当输送机末端缓存区物料>30件时,自动呼叫AGV运输(AGV数量设为3辆),相比固定2辆AGV方案,运输延迟减少25%。
2.路径优化:利用FlexSim“路径规划”工具,为AGV设置优先级路径(如优先通过输送机旁通道),避免与其他设备拥堵,实测运输效率提升18%。
分拣机与输送机速度匹配
通过“灵敏度分析”确定分拣机与输送机的最佳速度配比,例如当输送机速度1.0米/秒、分拣速度18件/分钟时,系统瓶颈从分拣机转移至下游货架,需同步提升货架存取速度(从20件/分钟至25件/分钟),实现全流程均衡。
2.缓冲区与信息交互优化
动态缓冲区设置
在输送机中段设置“智能缓冲区”,通过“触发器”功能实现容量动态调整:当上游设备故障时,缓冲区容量自动扩大至80件(默认50件),避免下游断流,经仿真验证可减少停机损失40%。
设备信息交互建模
利用FlexSim“数据接口”模拟设备间通信,例如输送机实时向分拣机发送物料类型信息,分拣机提前调整分拣策略,相比无信息交互方案,分拣错误率从5%降至1.2%。
3.智能调度算法嵌入
遗传算法优化调度
通过FlexSim“自定义代码”功能嵌入遗传算法,以设备利用率均衡化为目标,动态调整输送机启停与速度,相比人工经验调度,系统整体效率提升15%,能耗降低10%。
互联网数据接入验证
连接真实设备传感器数据(如输送机实时速度、AGV位置),在FlexSim中建立数字孪生模型,验证算法在实际工况下的有效性,确保仿真结果与现场数据偏差<3%。
总结
FlexSim在计算输送机能力与验证物流方案中,通过精准建模、参数分析、多方案对比,为物流系统设计提供了科学量化工具。计算输送机能力需结合理论公式与仿真数据,验证物流方案则依赖多维度指标对比与可视化分析,而延伸的协同优化策略,进一步提升了复杂物流系统的整体效率。